TEN32 Guitars Explained in 2 Minutes
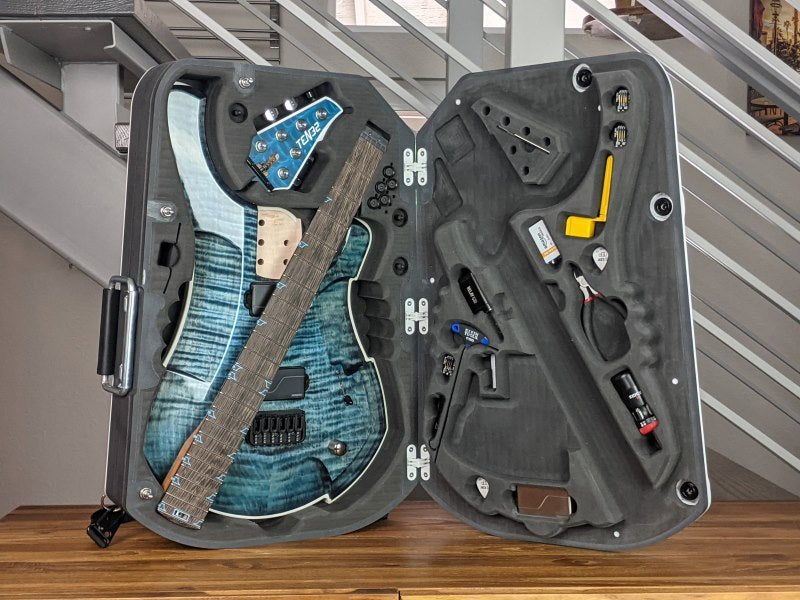
"What am I looking at?"
So you're curious what sets TEN32 Guitars apart? Here's the stiff one-line version that takes itself way too seriously:
TEN32 Guitars boldly challenge conventional design, achieving hyper-functionality with zero sacrifices.
"Hyper what now? WTF does that mean?"
We'll get there shortly. "Hyper-functionality" aside, what we can definitely agree on is that a guitar has to feel, play, and sound great, so we'll start with some social proof:
So what makes a guitar hyper-functional? Let's dive in.
1 - Modularity is the backbone of the whole system
Modular headstocks, necks, nuts, and electronics + non-destructive fasteners make TEN32 guitars intuitively easy to customize, maintain, and repair. It makes the instrument more durable, functional, and inspiring for you - the player - across it's entire life cycle.
"How's that work?"
By enabling you to quickly & easily swap parts without a tech for different specs (like neck scale length), different tones via solderless electronics, or even a new look by changing the headstock. If swapping parts isnt your thing, modularity isn't just for the player - it massively simplifies manufacturing.
I also offer swappable modular body and headstock finishes, which I'm sure sounds insane...more on that below.
2 - Portability is a happy accident
"Portability? Is this clown making travel guitars? Aren't they all shit?"
Yes they are! Which is why it's a good thing TEN32s aren't travel guitars. Portability is just a delicious modularity bonus. Turns out, a removable modular headstock is the perfect way to make all the parts of a full-size guitar small enough to fit in a purpose built backpack case - a case that's small enough to fit under an airplane seat, like these:
3 - A bolt-on headstock is just an option, like any other
If a bolt-on headstock makes you sweaty, I also build conventional necks, and they're 100% compatible with the rest of the system. You can swap between conventional necks and bolt-on headstock style necks anytime, but of course - conventional necks wont fit in the backpack case.
4 - A different approach to finishing
Finishing techniques haven't evolved for decades, so I developed some new approaches. The first is a machined epoxy finish. The goal here is to use CNC technology to precisely control finish thickness, add structure to impact-prone areas, and create textures that are visually appealing. They also avoid showing scratches & fingerprints, and dont stick to your skin.
Here's an example of a clear coat - I bet you can't tell the difference, but you'll see the texture if you click to zoom in:

If you want something even more radical, I also offer modular, printed aluminum tops. You read that right - modular guitar finishes. It works on headstocks too, and AI generated images are PERFECT for this application. Take a look at what's possible:
5 - A mountain of other improvements
The above covers the critical aspects, but I've also done my best to improve literally every part of the instrument. From jack mounting to restringing a Floyd, everything works better than what you're used to.
If you want more details and prefer to read, start here. If you prefer video, start here. If you want to build one and see what it costs, click here.