What's a resin finish?
In lieu of sufficient space and equipment to do traditional sprayed finishes, and in search of a guitar finish that offered new and unique features, I developed a technique using epoxy resins. These finishes are cured inside a temperature controlled pressure vessel, purpose built for the application.
If you have a confused look on your face right now, I don't blame you. So....why would one finish a guitar using resin? The main objective was to explore the one aspect of guitar finishes that we haven't already seen a million variations of - texture.
Lets take a look at the main aesthetic factors of a guitar finish.
Color - Nothing mind blowing here, every shade you can imagine has probably ended up on a guitar at some point.
Sheen - Most guitars are shiny, but there are plenty of matte, satin, etc options available. Pretty simple to achieve any of these. We've seen the spectrum of sheen explored fully.
Custom Graphics/Paint - There are infinite color schemes or thematic concepts that haven't yet ended up on guitars, but most of this work is clear coated and you're right back to shiny and smooth.
Wood grain - No explanation needed here. We've seen about everything wood grain has to offer.
There's absolutely nothing wrong with any of the above, but as you may have noticed, a big objective around here is to move the instrument forward in as many ways as possible, finishes included.
Texture - There are actually lots of examples of textured finishes out there, just not nearly as many as the more typical choices. There might only be one textured example for every 1000 shiny/smooth finishes. Exposed wood grain is probably the most common, usually using swamp ash since it has large dramatic grain patterns. Other examples include several textured finishes on the JEM series from Ibanez. "Relic'd" finishes can also offer some textural interest. I'm sure there are others.
The bottom line is simply the fact that texture offers the largest amount of unexplored territory vs any other "finish factor", which makes it attractive from the perspective of innovation.
Ok, that's one reason...what else?
Micro scratches, swirl marks, fingerprints, and skin stickiness are all problems for smooth finishes. The glossier the finish, the bigger these problems become. Sure, the guitar looks great the day you buy it but a week later you've experienced all of the above and will continue to for the life of the instrument. Is there a better way?
Yes! A textured finish suffers from none of these issues, and without any other sacrifices. If you were to see a textured TEN32 being played on stage, you'd never know it was textured at all. Its only visible up close and you'll never have to worry about any of the stuff listed above. Don't believe me? Take a look....these are photos of the same guitar:


In the 1st image, at a distance of just a few feet, its impossible to tell the surface has texture. You can only see the texture if you look closely and have sufficient light reflecting from the surface.
Engraving - plenty of engraved finishes have been done, but typically by either carving a relief directly into the wood, or laser engraving the wood surface. Both are usually just covered up with another shiny, smooth clear coat. Yawn.
Resin based finishes are often pigmented, which means they're the same color throughout, and can therefore be engraved directly into, as such:
Other benefits:
Semi-transparent resin - Wood grain and/or laser engraving under a semi-transparent resin finish provide a subtly unique look you're not likely to find anywhere else.
Design options - If you time it right, resins can be "drawn" into, and they'll actually retain the patterns imparted. You can even make resin look like wood grain, right down to the knots.
You can also "paint by numbers" with resin, simply cutting cavities and replacing wood with any number of colors, to create anything from simple designs to complex artwork. Pigments that absorb and re-emit light can be used for fret markers, bindings etc. This is the same headstock as above. The white binding has glowing pigment added:
You can also invert the effect. These two photos are of the same part!

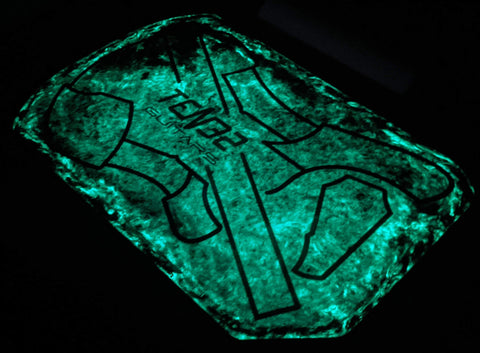
I mentioned bindings and inlays...its obviously much easier and infinitely more versatile to machine a cavity, then simply inject it full of liquid resin and allow it to cure vs the traditional approach to inlays or binding. Resin is typically MUCH harder than the wood surrounding it in this arrangement, so if you're concerned about resin fretboard inlays or binding wearing away, don't be!
You can also imagine the expanded color palette this approach offers vs normal inlays and binding in particular, as well as complete control of the thickness and width of binding. You can can even impregnate resin with metal powders or carbon fiber to create impact resistant bound edges.
Put simply, resin is far more interesting and versatile as a finishing tool, and solves many if not all of the problems traditional sprayed on finishes suffer from.
Finally, those of you who have attempted to use resin to finish a guitar before will know that it presents a long list of challenges and often comes out tacky, full of bubbles, or just leaves a huge mess. Figuring out resin has been my #1 biggest headache, but I managed to overcome all the issues with specialized equipment, tons of practice, and regularly screaming profanities.
Up next, lets explore exactly how TEN32 Guitars are assembled.